Measuring Process Efficiency and Effectiveness
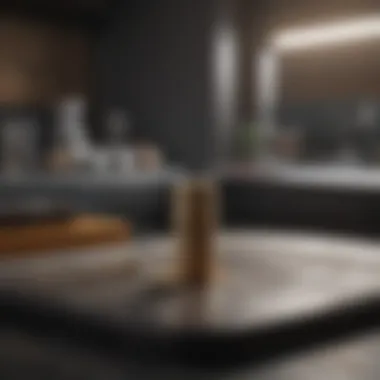
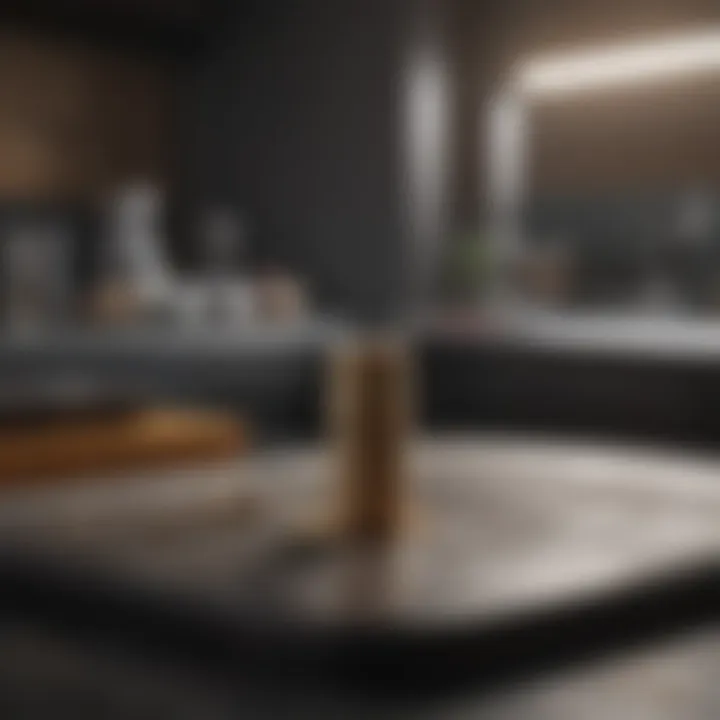
Intro
In todayโs fast-paced business landscape, organizations are constantly on the lookout for ways to optimize their operations. Understanding how to assess process efficiency and effectiveness emerges as a pivotal task. The distinction lies not merely in executing tasks faster but in whether those tasks contribute meaningfully to the organization's goals. Efficient process management ensures resources are allocated wisely, while effective practices guarantee that outcomes align with strategic objectives. Thus, having a grip on these two concepts can spell the difference between success and stagnation for any business.
Key Concepts and Definitions
A clear understanding of terminologies related to process assessment sets the groundwork for more profound analysis. This section breaks down the fundamental ideas that underpin assessments of efficiency and effectiveness.
Efficiency vs. Effectiveness
When dissecting operational practices, efficiency refers to how resourcesโtime, money, and manpowerโare utilized. It is about doing things right, minimizing waste to maximize output. On the other hand, effectiveness concerns the extent to which operations achieve their desired results. Here lies a fundamental question: can you achieve impressive efficiency without sacrificing effectiveness?
"Efficiency is doing better what is already being done; effectiveness is doing the right thing."
โ Peter F. Drucker
Understanding these distinctions is more than just academic; it translates into tangible results on the ground. For instance, a company may streamline its production process to enhance efficiency, but if the products fail to meet quality standards, it would indicate a failure in effectiveness.
Metrics for Assessment
A solid grasp of metrics is crucial when assessing processes. Certain indicators can shed light on how efficient and effective your operations are. These include:
- Cycle Time: Measures the time taken to complete a process from start to finish. A shorter cycle time generally indicates higher efficiency.
- Output Quality: Assess if the final product meets the established quality standards.
- Resource Utilization: Analyze how effectively resources are mobilized and consumed during operations.
- Customer Satisfaction: Gauge the end-user's perception of the product or service, an indirect measure of effectiveness.
Identifying these metrics helps in reviewing performance and spotting areas for improvement, transforming a vague understanding of efficiency and effectiveness into actionable insights.
Continuous Improvement
No process is flawless or static. Continuous improvement is a philosophy that organizations can adopt. It emphasizes ongoing efforts to enhance products, services, or processes by adopting incremental improvements. Techniques such as Lean and Six Sigma often feature prominently in discussions of continuous improvement. These methods focus on waste reduction and quality enhancement, significantly impacting organizational performance.
In this frame of reference, companies are encouraged to foster a culture where employees feel empowered to identify inefficiencies and contribute to solutions. This approach reinvigorates processes and cultivates a work environment that values adaptability and responsiveness to changing conditions.
Expert Insights and Advice
Acquiring insights from industry experts can accelerate understanding and application of the concepts discussed. These professionals often share valuable strategies that resonate with both novices and seasoned practitioners in the realm of process evaluation.
Data Analysis and Process Improvement
With the rise of big data, organizations now have richer datasets at their disposal. Data analysis tools can help make sense of these statistics. Correlating data points can lead to identifying trends that might not be immediately visible. It can also clarify performance metrics and guide decision-making.
Itโs surprising how data can reveal the unseen. For instance, a business may realize that customer complaints spike during certain hours, indicating a need for process adjustments during peak times.
The Role of Technology
Those organizations that embrace technology not only enhance immediate performance but build a foundation for scalable growth in the long run.
Understanding Process Efficiency and Effectiveness
In any organization, understanding process efficiency and effectiveness is akin to having a well-tuned engine under the hood; it keeps everything running smoothly or reveals areas in dire need of an overhaul. Itโs not just a matter of knowing what happens in daily operations. It encompasses a broader view, examining how resources are utilized and whether these efforts align with organizational goals.
Being aware of process efficiency allows companies to streamline their operations. This can save time, reduce waste, and ultimately lead to cost savings. In contrast, effectiveness speaks to whether those streamlined processes produce the desired outcomes. Focusing purely on efficiency could lead one down a path where short-term gains obscure longer-term goals. Therefore, balancing these two dimensions is crucial. Hereโs why:
- Improvement Opportunities: Regularly assessing processes enables organizations to pinpoint bottlenecks, redundancies, and underutilized resources. Identifying these areas can lead to substantial improvements that may not be immediately obvious.
- Competitive Advantage: In todayโs fast-paced business environment, being efficient and effective can set a company apart. Organizations that deftly balance these elements often outperform competitors, tapping into resources that others may overlook.
- Stakeholder Trust: Demonstrating that a company is committed to maximizing its processes fosters stakeholder confidence. Whether it's investors paying attention to financial efficiency or customers being served effectively, this clarity can lead to business sustainability and growth.
"An organization that measures its processes diligently doesn't just run a tight ship; it sets sail towards unexplored waters of opportunity."
The importance of understanding these concepts cannot be overstated. It fundamentally shapes how businesses approach their daily operations and long-term strategies.
The Importance of Measuring Processes
Measuring processes might seem like just another buzzword in the corporate lexicon, but it represents a fundamental aspect of organizational growth and sustainability. Without a clear understanding of how processes function, any decision made can quickly become a shot in the dark. Process measurement serves several functionsโit provides a lens through which an organization can appraise its performance, identify bottlenecks, and ensure compliance with established standards. Engaging in effective measurement is pivotal for any organization aiming for long-term improvement and adapting to the ever-changing landscape of market demands.
By prioritizing measurements, organizations can see tangible benefits such as increased productivity, optimized resource allocation, and better alignment of objectives across teams. While at first glance, this diligence may appear tedious, the dividends it pays in strategic decision-making, cost savings, and risk management make it all worthwhile.
Impact on Organizational Performance
When an organization takes the leap to measure its processes, it undergoes a profound transformation in its operational dynamics. Performance metrics can reveal trends and patterns that may otherwise remain hidden in the shadows of daily activities. The insights gained from data allow leaders to make informed decisions rather than relying on instinct or experience alone.
For instance, consider a manufacturing plant that implements performance metrics to measure the time taken for assembly line tasks. Soon enough, leaders might discover that a particular segment is lagging behind not due to worker inefficiency, but because of outdated machines that require more downtime for maintenance. By redirecting investment to upgrade technology, the plant not only enhances productivity but improves employee morale as well, turning frustration into efficiency.
"Data is like oil; it's valuable, but you must refine it to unlock its true potential."
Identifying Improvement Opportunities
Finding cracks in the system is a nuanced art, and measuring processes is the first step in this journey. When numerical data is gathered and scrutinized, areas for enhancement often bubble to the surface. This is where organizations can sift through the metrics and spot opportunities for fine-tuning.
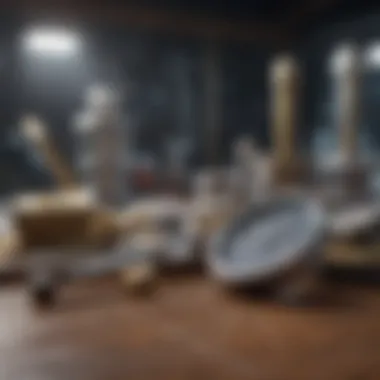
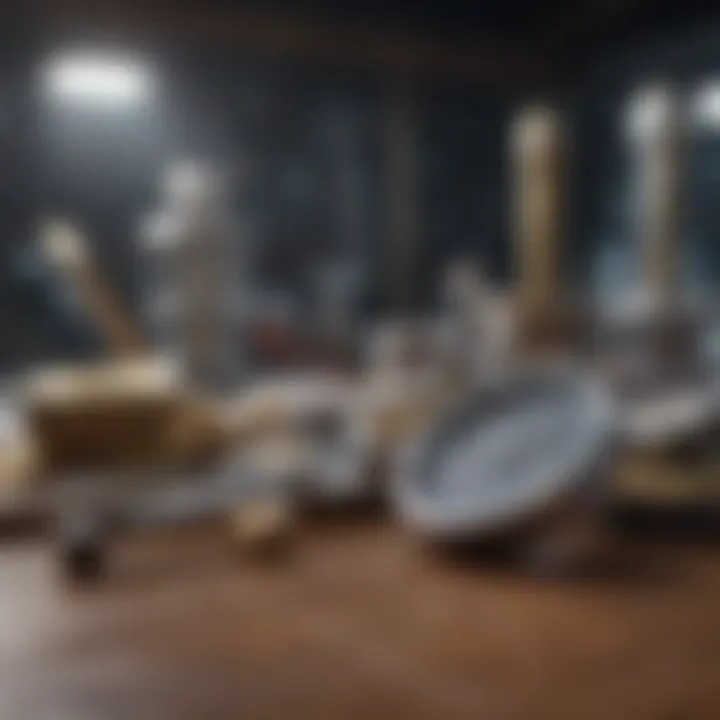
For example, a retail chain might analyze customer checkout times. By tracking this data, they may find that peak hours consistently see longer waits, primarily due to insufficient staff during busy times. Implementing additional staff during these hours would not only shorten lines but would also improve the overall shopping experience, boosting customer satisfaction and increasing return visits.
Moreover, establishing regular review cycles allows organizations to remain agile; continuous inspections often highlight recurring challenges that, if ignored, hinder progress. Addressing these issues proactively leads to more streamlined processes, which consequently elevate overall business performance.
Compliance and Risk Management
In todayโs regulatory environment, compliance isnโt merely a checkboxโitโs a survival strategy. Robust measurement allows organizations to stay aligned with industry standards and regulations, mitigating the risk of legal repercussions. By closely monitoring processes, companies can flag deviations before they spiral into compliance violations, resulting in fines or reputational damage.
Furthermore, effective risk management is intertwined with process measurement. By understanding which processes are most vulnerable to disruption, firms can develop contingency plans or investment strategies to bolster resilience. For example, a financial institution might assess its transaction approval process. If anomalies or delays crop up during particular transaction types, these lead to not only customer dissatisfaction but potential losses. Knowing this, the institution can focus on preventative measures that protect against financial and reputational risks.
In sum, measuring processes is not just an exercise in data collection; it's a nucleus around which informed decisions, compliance, risk management, and continuous improvement rotate. Organizations willing to take this critical step often find themselves better equipped to navigate challenges and seize new opportunities.
Metrics for Measuring Process Efficiency
Understanding metrics for process efficiency is akin to having a compass in a dense fog. It provides direction and clarity on where an organization stands in relation to its goals. Metrics offer a tangible means of monitoring performance, pinpointing areas for improvement, and ultimately maximizing productivity. When you dive into the metrics, you engage with two crucial components: data and benchmarks. In short, these metrics enable organizations to make informed, data-driven decisions that lead to better resource allocation and process enhancements.
These evaluations not only highlight performance but also act as a catalyst for change. When organizations track these metrics diligently, they uncover insights that are often missed on a surface level. It's essential to not just gather data but to analyze it in a way that yields actionable outcomes.
Commonly Used Efficiency Metrics
When it comes to measuring efficiency, a handful of key indicators should come to the forefront. These metrics serve as established guidelines, helping businesses gauge how well their processes are running. Some common metrics include:
- Process Cycle Time: This measures the total time taken to complete a process from start to finish. If cycle time is lengthy, it might indicate bottlenecks.
- Throughput: This refers to the number of units produced or services completed in a given timeframe. Itโs a straightforward way of tracking production capacity.
- Resource Utilization: This is calculated by dividing the actual output by the maximum possible output, showing how well resources are being employed.
- Overall Equipment Effectiveness (OEE): This combines availability, performance, and quality to provide a comprehensive measure of how effectively a manufacturing operation is utilized.
These metrics create a baseline for performance assessment. By continuously monitoring them, an organization can quickly identify hiccups and enhance process efficiency. The goal here is to align operational outputs with strategic goals.
Calculating Cost Efficiency
Cost efficiency is a vital piece of the puzzle in measuring process efficiency. It represents an organizationโs ability to deliver a product or service at the lowest possible cost without sacrificing quality. To calculate cost efficiency, consider the following approach:
- Identify all costs associated with the process, including fixed and variable costs.
- Divide total costs by the total output produced. This gives you a per-unit cost that can be analyzed over time or compared against industry standards.
For example, if a manufacturing plant spends $100,000 to produce 10,000 units, the cost efficiency formula would be:
By establishing cost-efficiency metrics, an organization can not only track its spending but also identify trends. It encourages a more savings-oriented mindset across departments, pushing for operational enhancements even when the budget looks tight. This proactive approach ensures financial health in the long run.
Time-Based Metrics
When evaluating process efficiency, time is of the essence. Tracking how long processes take and where delays occur can illuminate areas that require immediate attention. Key time-based metrics include:
- Lead Time: The total time from the initiation of a process to its completion. Reducing lead time is critical for keeping customers satisfied.
- Turnaround Time: This focuses on how quickly a process can be completed, which is essential in service-oriented organizations.
- Time to Value (TTV): This evaluates how long it takes for a customer to receive the value of a product after purchase, relevant in both service and manufacturing sectors.
Employing these time-based metrics allows organizations to ensure that they're not just effective in their processes but also efficient in their execution. A keen eye on these timing aspects enables quicker responses to market changes. Additionally, it fosters an environment where ongoing improvement becomes second nature.
In the race to enhance efficiency, measuring is not just important; it's essential. When organizations throw a spotlight on their metrics, they open the door to better decision-making and smarter resource utilization.
In summary, integrating these metrics into regular assessments can bolster process efficiency and set the stage for continuous growth and refinement.
Metrics for Measuring Process Effectiveness
Effective processes form the backbone of an organizationโs success. However, gauging how well those processes perform is crucial. Metrics for measuring process effectiveness provide insights that help organizations stay on track toward their goals. In this article, we'll focus on these metrics, their specific elements, benefits, and considerations that organizations must keep in mind.
At its core, measuring effectiveness is all about determining whether a process achieves its intended outcomes. By analyzing these factors, organizations can not only understand their current performance but also identify areas ripe for improvement. This is particularly vital in todayโs fast-paced business landscape, where stakeholder satisfaction can often make or break a company.
Key Performance Indicators (KPIs)
Key Performance Indicators, or KPIs, act like beacons guiding organizations toward their strategic objectives. These measurable values indicate how effectively a company is achieving its key business goals. Different organizations may have varying KPIs depending on their specific objectives and industry standards.
Consider a tech startup that focuses on launching new software. Their KPIs might include:
- User Acquisition Rate: Measures how quickly they can attract new users to their platform.
- Churn Rate: Indicates the percentage of users who stop using the service, providing insights into user satisfaction.
When effectively defined and tracked, KPIs enable organizations to:
- Align activities with strategic goals: KPIs ensure that everyone in the organization understands the primary objectives and can work towards them.
- Provide focus on performance: By spotlighting specific metrics, organizations can identify areas needing attention.
- Facilitate informed decision-making: KPIs derive from data, allowing for objective evaluation and trend spotting.
Tools and Techniques for Measurement
Acquiring a strong grasp of tools and techniques for measurement is crucial for assessing both efficiency and effectiveness within organizations. These methodologies lay the groundwork for insightful analysis and informed decision-making. Engaging with the right tools enables businesses to visualize their processes, scrutinize performance data, and refine operations. From process mapping to data analytics, it all boils down to whether an organization can use these techniques effectively to enhance productivity and minimize waste.
Process Mapping Techniques
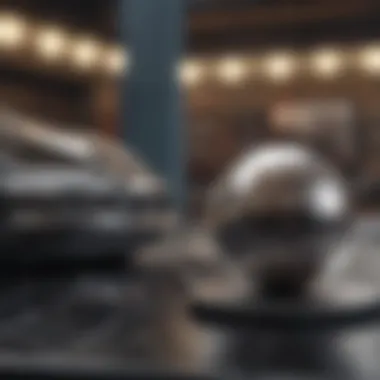
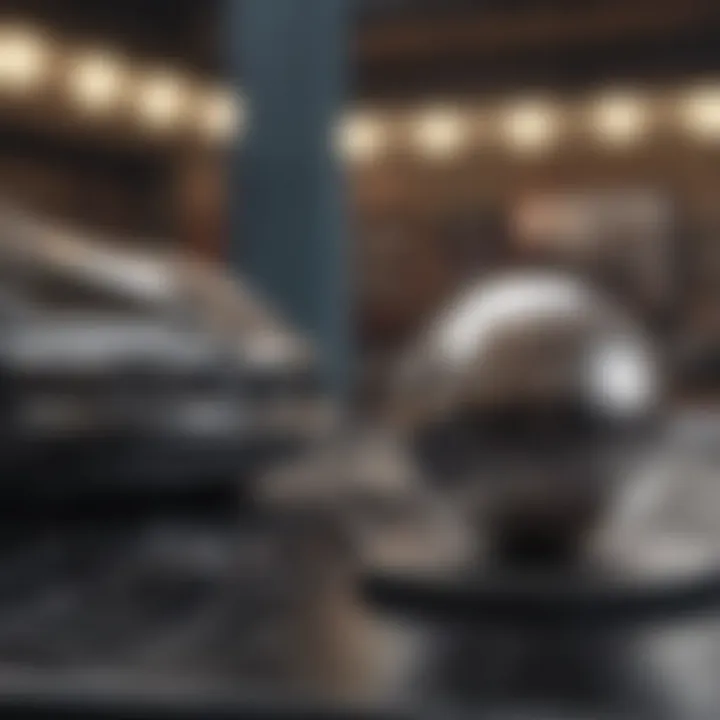
Process mapping techniques encompass a series of methods that visually depict the steps involved in a given process. They help to clarify how tasks interlink, making it easier to identify bottlenecks and redundant tasks. By taking these in-depth snapshots of workflows, organizations can streamline operations, thus amplifying efficiency. The benefits of utilizing process mapping include:
- Clear Visualization: Diagrams offer a straightforward representation of complicated processes, making them easier to understand at a glance.
- Identifying Redundancies: Through mapping, organizations can spot unnecessary steps in a process, paving the way for optimization.
- Collaborative Insight: Engaging teams in the mapping process encourages different perspectives and shared ownership of the workflows.
In practice, tools like Lucidchart or Microsoft Visio can be instrumental. They provide templates and drag-and-drop features that can save time while ensuring clarity.
Data Analysis and Performance Dashboards
Data analysis forms the backbone of informed decision-making. Performance dashboards visualize key metrics, turning raw data into actionable insights. These dashboards aggregate information from various sources and present it in a user-friendly format. Here's why they are vital:
- Real-Time Insights: Dashboards provide up-to-the-minute data, allowing agile responses to emerging issues.
- Customized Metrics: Organizations can tailor dashboard metrics to focus on specific performance benchmarks crucial to their objectives.
- Enhanced Communication: A well-designed dashboard can convey complex information to diverse stakeholders, minimizing misunderstandings.
For those looking to delve deeper into data analysis, tools such as Tableau or Power BI offer robust functionalities, including interactive visualizations and predictive analytics, which help organizations maintain a competitive edge.
Lean and Six Sigma Methodologies
Lean and Six Sigma are methodologies rooted in process improvement with specific focus areas. Lean seeks to eliminate waste, while Six Sigma emphasizes reducing variation and defects. When combined, they contribute significantly to process efficiency and effectiveness.
- Continuous Improvement: Both methodologies advocate for ongoing refinement of processes, ensuring that efficiency and effectiveness are not just buzzwords but continuous goals.
- Employee Engagement: These methodologies often involve employees at all levels, fostering a culture that values improvement and excellence.
- Structured Problem Solving: Lean and Six Sigma provide structured frameworks for tackling issues, making it less daunting for organizations to face challenges head-on.
Incorporating tools such as DMAIC (Define, Measure, Analyze, Improve, Control) helps structure the approach to problem-solving, guiding organizations in achieving sustainable results.
"Measurement is not just about quantifying. It's about understanding the whole process of work and where improvements can be made."
The Role of Technology in Measurement
In todayโs frantic business environment, technology plays a pivotal role in measuring process efficiency and effectiveness. This segment dissects how tech influences the accuracy of assessments and boosts the overall evaluation process. With the advent of advanced tools, organizations can streamline data collection and analysis, making the entire process more systematic and reliable. Moreover, embracing technology often leads to better decision-making by providing clearer insights into operational performance.
Automation in Data Collection
The automation of data collection marks a significant shift from traditional methods that often involve time-consuming manual input. Automated systems capture data at high speeds, reducing the likelihood of human error; after all, a small mistake in data entry could lead to erroneous conclusions.
Data can flow seamlessly from various sources, including transactions, customer interactions, and supplier engagements, into centralized platforms. For instance, Customer Relationship Management (CRM) tools automatically gather customer data like purchase history and feedback, freeing up resources that can be allocated elsewhere.
Benefits of Automation in Data Collection:
- Time Efficiency: Saves labor hours by minimizing repetitive tasks.
- Accuracy: Reduces human errors in data entry and processing.
- Consistency: Ensures uniformity in the data collection process, producing reliable insights.
Automation can make real-time decisions possible, which is key in fast-paced sectors where every second counts.
Real-Time Monitoring Systems
Real-time monitoring systems revolutionize how organizations assess efficiency and effectiveness. They provide instant feedback, allowing businesses to track performance against defined metrics as soon as events unfold. For example, in a manufacturing setting, sensors can provide updates about machine performance and production rates, enabling quick interventions before small issues escalate.
Such systems not only enhance visibility into operations but also offer flexibility in making immediate adjustments. Rather than waiting for end-of-month reports, leaders can view daily or even hourly metrics and thus can identify trends or anomalies almost instantly.
Key Elements of Real-Time Monitoring:
- Immediate Access to Data: Offers organizations up-to-the-minute insights into processes.
- Proactive Decisions: Enables quick corrective actions to keep processes on track.
- Comprehensive Dashboards: Visual representations of performance metrics aid in understanding complex data easily.
These systems can foster a more responsive organizational culture, encouraging teams to act swiftly and decisively.
Impact of Artificial Intelligence on Process Evaluation
Artificial Intelligence (AI) is reshaping how companies approach process evaluation. By leveraging algorithms and machine learning, businesses can analyze vast amounts of data far quicker than a human could. AI can identify patterns that might go unnoticed and forecast potential problems long before they arise.
Applications of AI in Process Evaluation:
- Predictive Analytics: Anticipates future outcomes based on historical data, allowing businesses to plan accordingly.
- Anomaly Detection: Spotting irregularities helps pinpoint inefficiencies or malfunctions that might threat overall effectiveness.
- Automated Reporting: Generates insights and presentations automatically, reducing the burden on staff and allowing them to focus on higher-level strategic planning.
By embedding AI in their measurement practices, organizations can move towards a future where decisions are data-driven rather than intuition-based, enhancing their ability to navigate complex operational landscapes effectively.
Technology significantly improves the precision and speed of process evaluation while reducing the margin of error - a critical advantage in competitive markets.
Challenges in Measuring Efficiency and Effectiveness
Measuring how well processes run in an organization isnโt a walk in the park. The complexities involved in assessing efficiency and effectiveness demand a deep dive into a labyrinth of data, behaviors, and organizational dynamics. Overcoming these hurdles is fundamental to achieving operational excellence. If an organization cannot accurately measure these elements, even the most well-intentioned improvement strategies can miss the mark entirely.
Data Quality and Accessibility Issues
Data can be, more often than not, a double-edged sword. On one hand, quality data is a game-changer for performance assessments. On the other, poor data quality hampers decision-making. When data is riddled with inaccuracies or lacks sufficient context, it can lead to misguided conclusions about how processes are really performing.
- Inconsistent data collection methods can lead to erroneous conclusions. For example, if one team records data manually while another uses automated systems, comparing their outputs becomes tricky.
- Access restrictions also play a critical role in measuring. If key personnel can't access essential data because of bureaucratic red tape, it means decisions can be delayed or even based on incomplete information.
- Data overload is another challenge. A vast array of metrics can create confusion, making it difficult to discern what truly matters.
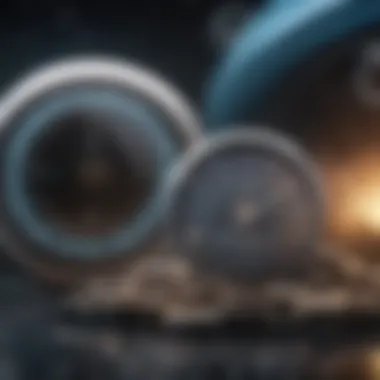
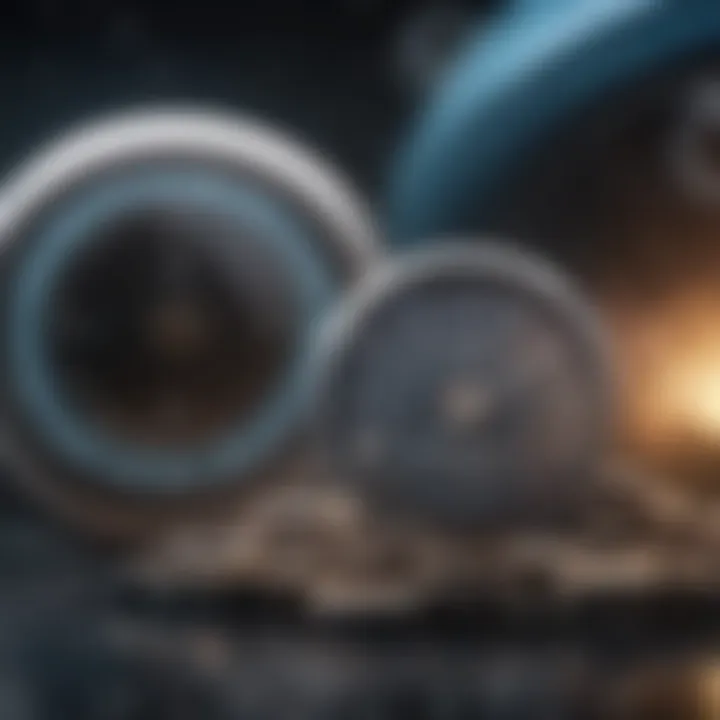
Addressing these issues requires a solid data governance framework that ensures data accuracy, accessibility, and usability. Time and resources are at stake here, and without a well-thought-out strategy, organizations may find themselves chasing their tails rather than making real progress.
Resistance to Change Within Organizations
One of the toughest nuts to crack in any organization is resistance to change. Even when data clearly points out inefficient processes, the human factor often gets in the way. When employees are set in their ways, the adoption of any new measures can feel like pushing a boulder uphill.
- Cultural inertia can undermine even the best metrics. For example, if frontline staff are accustomed to manual processes, shifting them to automated systems might lead to friction or pushback.
- Fear of the unknown is palpable. Employees may worry that changes in process will lead to job losses or added pressure. As a result, they may oppose initiatives that aim to improve efficiency.
- Lack of clear communication from leadership often exacerbates the problem. If the rationale for changes isnโt clearly articulated, skepticism reigns supreme.
A systematic approach to change management can alleviate these challenges. Getting managerial buy-in and ensuring people understand the benefits of new practices creates a smoother path toward acceptance.
Balancing Between Efficiency and Effectiveness
Striking the right balance between efficiency and effectiveness is akin to walking a tightrope. Organizations may be tempted to focus solely on streamlining processes, potentially neglecting the broader goal of meeting customer needs or achieving strategic aims.
- Too much emphasis on efficiency can lead to a superficial approach. For instance, a company might reduce costs by cutting corners, which ultimately results in quality issues and unsatisfied customers.
- Focusing only on effectiveness can lead organizations to fall into a trap where they are excellent at meeting high-level goals but inefficient in resource utilization.
- Finding the sweet spot requires organizations to constantly assess performance metrics in tandem to ensure that neither aspect is compromised. The ideal scenario is to enhance efficiency while ensuring effectiveness does not take a back seat.
"In the world of process improvement, balancing efficiency and effectiveness is crucial. One without the other can lead to diminished returns."
An organization's ability to measure these facets accurately will dictate its long-term success. As industries evolve, the need for refined processes alongside effective solutions is ever more pressing. This delicate equilibrium, albeit challenging, is essential for driving sustainable growth.
Implementing Continuous Improvement
Implementing continuous improvement is essential in the context of process efficiency and effectiveness. It serves as the backbone of any organization aiming to thrive in a competitive environment. By fostering a mindset oriented towards progress, organizations can sustain long-term growth and innovation. Continuous improvement isnโt just a one-time endeavor; itโs a perpetual cycle that incorporates feedback, the benchmarking of practices, and cultivating a proactive culture. This commitment to improvement enables organizations to adapt to changes and tackle the challenges of the modern marketplace.
The Role of Feedback Loops
Feedback loops signify a crucial aspect of the continuous improvement journey. They create a structured mechanism whereby performance metrics and outcomes inform future actions. Feedback can come from various sources, such as employees, customers, or even automated data systems. The integration of feedback allows for real-time adjustments, ensuring that processes remain sharp and focused on achieving desired results.
- Types of Feedback:
- Employee Feedback: Insights from those who are directly involved in the processes.
- Customer Feedback: External opinions that highlight areas of improvement from the consumer's standpoint.
- Performance Metrics: Quantitative measures that serve as indicators of success or failure.
The continuous flow of information helps ensure that no stone goes unturned in the analysis of efficiency and effectiveness. This iterative process empowers decision-makers to fine-tune processes and eliminate inefficiencies before they escalate into major issues.
Benchmarking Best Practices
Benchmarking is a pivotal tool in refining processes. By comparing organizational performance metrics against best practices from industry leaders, companies can gauge their standing in relation to their peers. The key is not only to identify what successful competitors do differently but also to understand and adapt those practices within oneโs unique context.
- Steps in Benchmarking:
- Identify Key Metrics: Focus on the specific metrics that matter most for your processes.
- Select Benchmarking Partners: Choose organizations renowned for their efficiency in the relevant field.
- Analyze Gaps: Assess where your organization falls short in comparison.
- Implement Changes: Integrate learned practices into existing workflows to spur improvement.
- Monitor Progress: Review the outcomes to see if changes yield the desired results.
Through benchmarking, organizations can gain a clearer understanding of their operational strengths and weaknesses. It encourages a culture of learning and innovation, where improvement is continuously sought.
Cultivating a Culture of Improvement
The essence of continuous improvement lies in fostering a culture that promotes it at all levels of the organization. This culture demands participation and buy-in from all employees, which can be challenging but rewarding.
- Strategies for Cultivation:
- Open Communication: Facilitate discussions around improvement opportunities in a constructive manner.
- Reward Systems: Recognize and reward employees who contribute to process enhancements.
- Training Programs: Invest in development to equip employees with skills for identifying and implementing improvements.
- Leadership Support: Ensure that leadership is visibly committed to improvement efforts, setting an example for the entire organization.
Creating such a culture leads to empowered employees who feel that their contributions matter. They become active participants in the journey towards greater efficiency and effectiveness, embracing changes rather than resisting them.
Ultimately, implementing continuous improvement is not merely a strategyโit's a philosophy that enables businesses to thrive amidst the complexities of modern industries.
Case Studies: Successful Measurement Practices
Understanding how organizations have effectively measured process efficiency and effectiveness provides invaluable insights. Case studies serve as practical examples of best practices, showing what works and what doesnโt in the real world. They highlight specific methodologies used, challenges overcome, and the tangible benefits that emerged from rigorous measurement.
When we examine these real-world situations, we gain context, making abstract concepts more relatable and actionable.
Industry-Specific Examples
Taking into account different sectors, we see an array of approaches. Letโs consider manufacturing, where just-in-time (JIT) inventory systems have been implemented. Companies like Toyota have mastered this technique, showcasing that aligning production schedules with inventory delivery can vastly improve efficiency. Their meticulous tracking of production lead times illustrates a profound understanding of both effectiveness and efficiency.
In the healthcare sector, looking at the practices of Cleveland Clinic demonstrates how focusing on patient outcomes has transformed their service delivery. They measure various effectiveness metrics like patient recovery rates and satisfaction surveys, which directly tie to their operational processes affecting both patient care and resource allocation.
For retail, the implementation of Point of Sale (POS) systems enables real-time inventory management. A notable example is Walmart, utilizing advanced data analytics from checkout systems to optimize stock levels and shift merchandise as required based on purchasing trends. This adaptive strategy increases efficiency by ensuring products are available when and where customers want them, thus enhancing customer satisfaction.
Lessons Learned from Notable Failures
Not all case studies end on a high note; examining missteps can reveal a landscape of lessons. A prominent example is Kodak, which struggled to adapt to the digital revolution. Their failure to measure and act effectively on changes in consumer behavior illustrates how neglecting to analyze market trends led to inefficiency in their processes.
Another cautionary tale is that of Blockbuster. Once a giant in the video rental industry, their inability to assess the effectiveness of emerging streaming services saw them lose out to more agile competitors like Netflix. This case highlights the crucial need for organizations to stay informed and receptive to evolving industry landscapes.
"Failure is simply the opportunity to begin again, this time more intelligently." โ Henry Ford
The significance of these industry-specific examples and notable failures lies not just in their outcomes but also in the methodologies used in assessing processes. Organizations can extract worthwhile insights, adapting strategies that might work for their unique settings. By observing these practices, entities can develop a comprehensive evaluation framework that drives significant improvements in productivity and customer satisfaction.